A fully autonomous takeoff and landing demo. The plane is designed and scratch-built specifically to be flown by the ArduPlane system. It has large control surfaces and a landing gear with a lot of suspension travel to work well on my local flying field with is a bit bumpy. My goal with this project is to create a plane that can fly waypoint missions and takeoff and land reliably in autonomous mode. This video was recorded in September of 2020, and a will continue to experiment and improve the plane. Lidar altitude sensor and airspeed sensor is comming…
I built this plane at the beginning of 2020. I started making a few first test flights in the spring. Then in April, almost exactly one year ago, unfortunately, some technical problems caused the plane to crash. The Chinese Pixhawk-clone I was using suddenly stopped working at an altitude of about 50 meters. The plane made a steep dive at high speed into the ground. The autopilot was fried, and it probably sent out full battery voltage on the 5V-bus in the process because the GPS, airspeed-sensor and telemetry-radio also get destroyed. I have a log-file with a large current-spike happening half a second before it died, in the air. The battery, motor, ESC, and all servos survived. But It was still a major setback for the project.
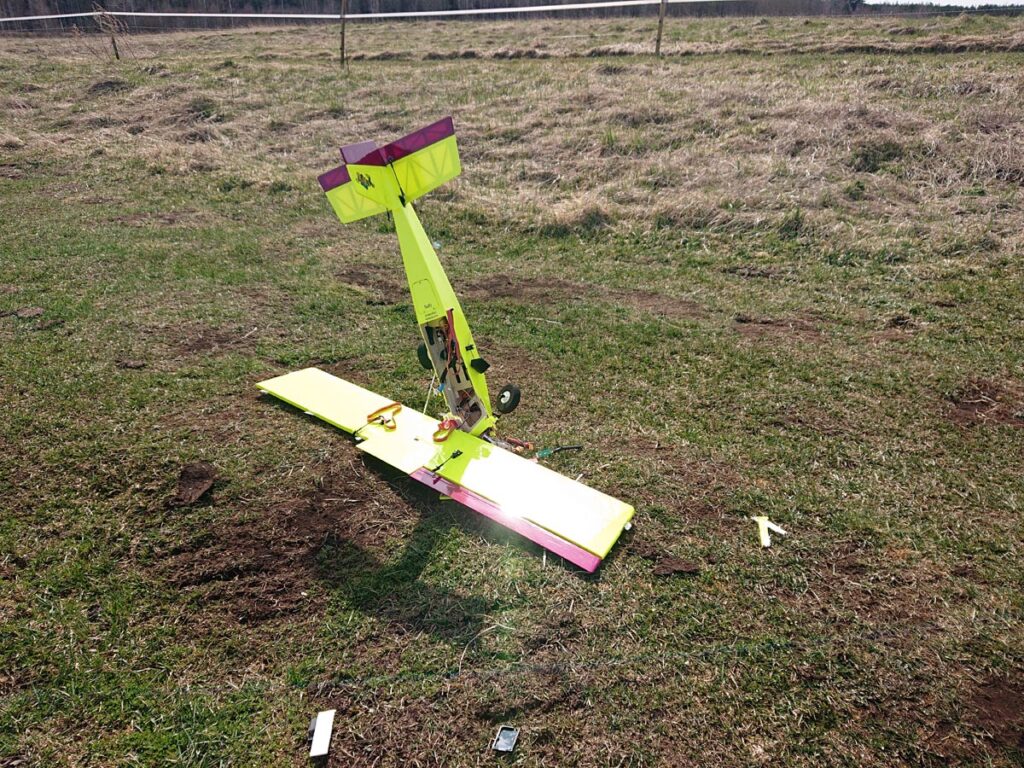

3-4 mounts later I decided to repair the plane and order new electronics for it. I am using a different Pixhawk-clone now, and I have made many successful flights with the plane. It has now logged over 10 hours in the air.